Low-cost satellite-based remote CP monitoring of pipelines
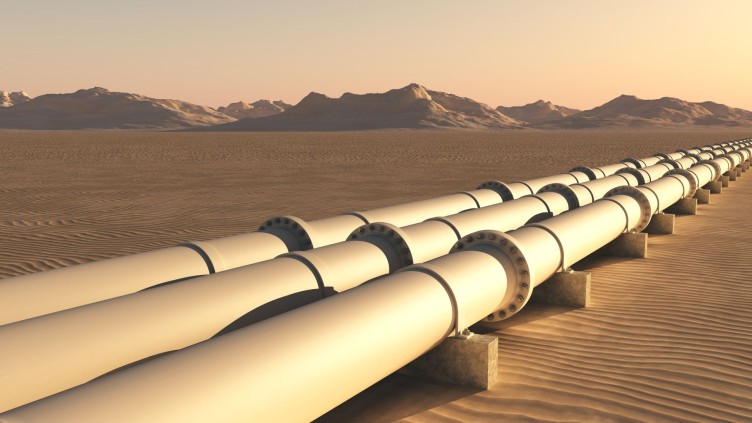
How IoT is ushering in a new era of cathodic protection for pipelines
Pipelines provide some of the most critical infrastructure in society, stretching over thousands of kilometres often in very inhospitable terrains. Two major challenges for pipeline operators are leaks and corrosion. Traditional metering and monitoring techniques for the cathodic protection of pipelines are costly and time consuming. Here, David Celine, managing director of remote monitoring specialist Omniflex, explains how low-cost satellite technology is ushering in a new era for IoT based pipeline monitoring.
According to Future Market Insights, “pipelines remain the top application in the global cathodic protection market. The segment is anticipated to generate more than 22 per cent of the global market share and will gain 90 basis points by the end of the forecast period [2022-2032].”
Despite this, much of the innovation in impressed current cathodic protection (ICCP) systems has been limited to structures such as wharves, ports, bridges, tanks and other more complex concrete and steel buildings. New technologies such as switch-mode based ICCP systems have become more popular for these applications because it is better suited to smaller currents driving more individual zones of protection. Switch-mode technology is also more suited for use in concrete applications, where the current outputs are lower, and more zones are required to achieve more uniform protection over the structure.
In contrast, pipelines that run thousands of kilometres still tend to rely on simple yet reliable transformer/rectifiers (T/Rs) producing a single large output voltage, often hundreds of Amps, more suited to the single large structure of the pipeline. Here, the T/R is placed at pump stations situated along the length of the pipeline. Cables then run from the T/R to anode beds of high silicon cast-iron or mixed metal oxide, which are buried in the ground a short distance from the pipe dependent upon the resistivity of the soil.
Sometimes the T/Rs are oil-cooled, rather than air-cooled, especially for pipelines that are transporting hazardous materials like gas, oil or petrol, for example to keep them explosion proof.
In either case, these T/Rs must deliver sufficiently high levels of current over long distances, to overcome voltage drops to the anodes and maintain a standard potential of 0.8 V below earth potential to supress corrosion. For example, a recent application we quoted for in the Middle East required around two dozen T/Rs each with a power output of 10 kW (100 V / 100 A).
This is a relatively high output, given that most building-based applications require only 5-10 V to protect against large voltage drops. However, pipeline CP systems can experience significantly higher voltage drops than other applications. In most cases, for accessible portions of overground pipelines, the voltages are ideally kept under 50 V to be deemed safe to touch.
Because longevity and reliability are essential in pipeline applications — and because any overhaul is prohibitively costly — many of these ICCP systems still rely on early-generation T/Rs. Despite the availability of newer-generation phase-control technology that allows the T/R’s output voltage to be adjusted linearly using a knob, many still rely on much older, simpler T/Rs where the output voltage is adjusted by using mechanical tap changers on the transformer that allow for variable turn ratios to be selected on the primary or secondary winding.
Measuring corrosion
Once the CP system is in place, one of the major challenges for operators is making sure that the pipeline is protected along its entire length. Suppressing the potential of the structure relative to earth using a T/R is not the difficult task; showing that it’s delivering ongoing protection is ultimately the more costly and time-consuming activity.
Firstly, the T/Rs need to be regularly inspected. Here, the feeds going from the T/R to each anode can be measured to ensure that not only is the T/R producing current, but that there is continuity to each anode. It’s important to check the connection to the anode to check that it is receiving current, as it could have been damaged as a result of farming activity or have corroded to the point of requiring replacement. The technician will use this opportunity to also check T/R coolant levels and operating temperature, as many are oil cooled.
The second test that is carried out is an instant-off potential test, which measures the electrical potential along the pipeline relative to stable reference electrodes placed in the soil near the pipeline. The DC current applied to the pipeline from the T/R polarises the pipe’s surface and suppresses corrosion. To take the reading, the current is turned off, and the potential difference between the pipeline and reference electrode is measured at the instance of turn-off, after the current is turned off, but before the potential of the pipe has had a chance to change. This is called the "instant-off" potential.
Typically, this requires a CP technician to drive the full length of the pipeline, perhaps as often as every few weeks depending on the product carried in the pipeline. As well as generally surveying the pipeline for visible signs of damage, such as fallen trees, evidence of leaks, vandalism and theft, the technician will take reference potential readings along the pipeline typically about every kilometre using test posts installed at regular intervals. A test post is often a three-inch pipe that protrudes from the ground with a junction box on the top containing connections to the pipe and to a reference electrode buried in the soil near the pipe. By recording the potential of the pipe at these known intervals (often manually), a profile of the corrosion risks on the entire pipeline can be determined.
This measurement allows the true corrosion potential of the pipeline to be measured accurately without the influence of the polarising current, which can skew readings and not provide a true reflection of whether the structure is being protected. By comparing the instant-off potential to the initial potential measurement, the effectiveness of the cathodic protection system can be determined.
Traditionally, this instant-off measurement was achieved by cycling the T/R on and off, for example every fifteen minutes, with the CP technician driving from one test post to another, using their watch to wait for the next off-cycle and taking the reading as soon as they detected a voltage drop. Thankfully, in recent years, this has been largely automated by using GPS receivers to allow a reading to be automatically taken at each test point and stored.
However, technicians are still needed to drive to each test-pole to manually retrieve the stored measurement data. This is because, while GPS receivers can be used to accurately take the reading, weak mobile reception in these often remote locations means that conventional GSM technology can’t reliably be used to remotely relay the collected data.
This is no more apparent than in my home country of Australia. According to research from ClientSAT, “Mobile phone services currently reach 99 per cent of the Australian population where people live. However, coverage is only available to around 27 per cent of the Australian landmass.” This makes it difficult to obtain test measurements from areas of pipeline that don’t follow roads or are otherwise easily accessible.
Using IOT in Pipline CP
To date, using satellite communications has posed an expensive solution to the problem of remotely monitoring CP data from pipelines. Access to the subscription plans for these high-orbiting satellite systems has traditionally been a barrier for pipeline operators, especially given that the data only needs to be collected periodically. These plans typically start around $35 p/m but can be as high as $99 p/m to track a higher number of nodes with a higher messaging allowance.
However, recent advancements in satellite technology, such as those offered by companies like Astrocast, Myriota and Swarm, are for the first time enabling low cost IoT applications to flourish. These so-called shoebox-sized satellites provide low-bandwidth satellite connectivity using ultra-small satellites in a low-orbit. The costs of these services can be as low as $5/month making it feasible to monitor pipeline applications.
Also, because these satellites make use of a low-orbit, the ground-based transmitters don’t require large antenna systems or a mains power source to work. Mains power does not run the length of the pipeline and is only available at points such as pump stations, and having large antennas can put the system at risk of theft or vandalism. As such, it’s preferable to have devices that can run on 10-year batteries and made compact enough to fit inside the tube of the test-post.
It was this leap forward in satellite technology that allowed Omniflex to develop the PowerView C1 CP Test Point Monitor. This device is ideally suited to remotely monitoring test posts on CP pipelines. It’s small enough to fit inside the three-inch test-post riser, runs on a 10-year lithium battery that would allow readings to be sent every two weeks and can be remotely configured using the PowerView CP web portal.
The PowerView C1 CP can be setup to take different measurements, including pipe-to-soil, bond current, and foreign structure potential. Depending on the setup, its input voltages range from -300 mV to +60 V AC and DC, making it ideal for pipeline applications. The device measures in at just 35 x 35 x 110 mm with a packed weight of just 150 g and has an ingress protection rating of IP67.
A new era of monitoring pipelines
These breakthroughs will increasingly eliminate the need for pipeline operators to send technicians out to manually collect measurements. Having more frequent access to CP data will also allow maintenance engineers to better manage their asset portfolio by only responding to events that require attention, thereby reducing their maintenance costs. These IoT solutions will also allow better management of more specialised CP applications like thickness testing on water pipelines, where the corrosion occurs on the inside surface of the pipeline.
What to do next
Read more about cathodic protection and remote monitoring technology for pipelines on the Omniflex website.
Stay in touch with us on LinkedIn!
Copyright © 2020 Omniflex (Pty) Ltd, All rights reserved. For further information, please contact us on: sales@omniflex.com or visit our website at www.omniflex.com
Comments
Display comments as Linear | Threaded